‘Like pushing toothpaste through a tube’. In a hydraulic system, there are two major components – a pump and a ram. The pump is usually (but not always) housed in its own cabinet and is sited near to the lift. It is powered by electricity. When the user presses the ‘Up’ button, the electric pump forces hydraulic fluid (oil) from a reservoir (tank), along a pipe (hose) to the ram which is situated between the lift guide rails. This pressurised fluid, forces a piston within the ram to extend in length and as it does so, the lift platform is pushed upwards. This self-lubricating drive method is efficient, smooth in operation and uses almost no energy when the lift is descending, as it relies only on gravity to close the ram and push the hydraulic fluid back to the tank. Hydraulic systems have some distinct advantages; firstly the lift can be easily lowered in the event of a power or equipment failure as you need only to manually open a valve at the pump end (like opening a tap). Secondly, as the pump is situated away from the lift, as opposed to being an integral part of it, the lift structure is very narrow and can fit into very tight spaces. Lastly, hydraulic drive units are supremely powerful, robust and reliable – you will have seen hydraulics on digger arms for example. They are generally underutilised on Platform Lifts and as such require minimal maintenance.
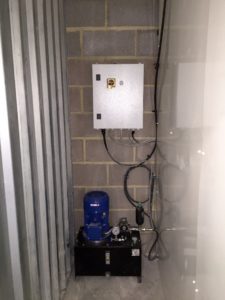
Hydraulic Pump and tank on floor / controller above

Hydraulic ram (between Guides)